Aluminum Car Parts: Exploring Its Process, Benefits, and Applications
In this long post by the aluminum parts manufacturer, we will be discussing how aluminum automobile parts are produced, their key benefits, and looking at the several applications in the several systems of vehicles.
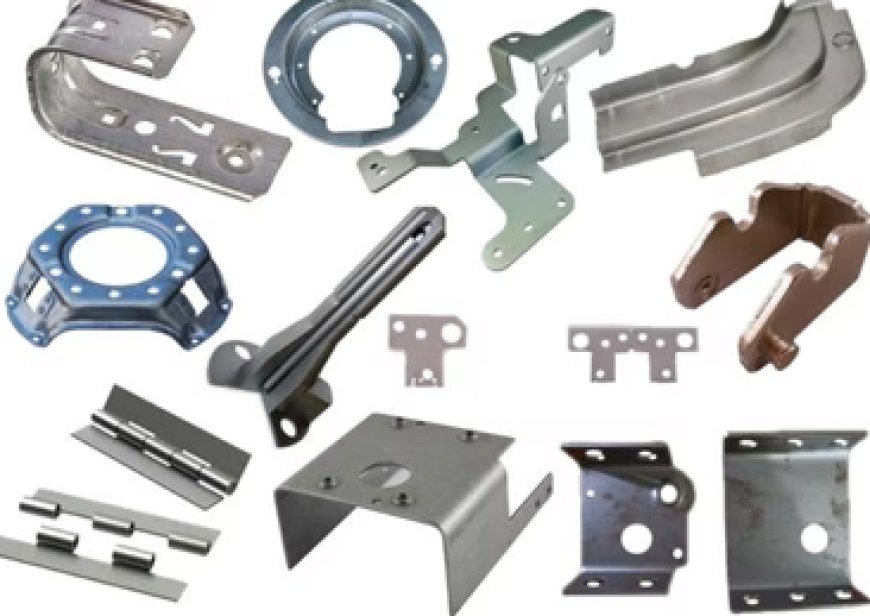
The automobile business is always evolving, and then there is that particular metal that more and more has been used in preference for the new car construction—aluminum. Because it is light, resistant to corrosion, and has a high weight-to-strength ratio, aluminum more and more has been used to take the place of heavy metals like steel to manufacture automobile components. As a result of ongoing care for the world and for mileage on gasoline, aluminum also has seen its time in the sun.
In this long post by the Aluminum Parts Manufacturer, we will be discussing how aluminum automobile parts are produced, their key benefits, and looking at the several applications in the several systems of vehicles.
Why Aluminium? Why the Increasing Demand in Automobiles
Steel was generally the material of choice utilized in automobile manufacturing for strength and economy. With increasing pressure on auto engineers to constantly push efficiencies and performances higher, however, the utilization of aluminum is being asked to play an increasingly larger role.
The Aluminum Association reports per-vehicle use of aluminum is up over 30% in the past decade. Aluminum facilitates cleaner emissions and better fuel economy for light metal and enables it.
The Process: How Aluminum Car Parts Are Created
Manufacturing car parts made of aluminum is a multi-step process—transitioning from digging up raw material to making the finished product. The following are the most important steps:
1. Refining and Extraction
Aluminum is extracted from bauxite ore in a two-step process:
- Bayer Process: The bauxite is purified to produce alumina (aluminum oxide).
- Hall-Héroult Process: Alumina is electrolyzed to produce pure aluminum.
2. Alloying
Aluminum is very brittle in its pure state and provides no strength, and so it usually is alloyed with metals like magnesium, silicon, or copper for hardening and strengthening them. Aluminum alloys are created with some definite, surefire attributes of performance to use them in cars.
3. Forming Processes
Components of cars produced using aluminum are created by different processes of forming in order to match some components to some applications:
- Casting: Aluminum metal is melted and cast into mouldings to create engine blocks, cylinder heads, or transmission housings.
- Extrusion: Aluminum billets are extruded through dies to create long components such as crash rails and bumper beams.
- Stamping: Aluminum sheets are stamped out to create body panels such as doors, hoods, and fenders.
- Forging: Aluminum is forced at high pressure to create hard, heavy-duty pieces such as suspension components.
4. Machining and Assembly
They are machined to specifications after being cut and fitted into position to form subsystems. Dimensional accuracy is achieved by CNC machines, particularly in parts that need close tolerance.
5. Finishing
- Aluminum parts can be treated on the surface with
- Anodizing for corrosion protection
- Paint or powder coating for improvement in appearance
Advantages of Aluminium Car Parts
The shift towards aluminum comes with a variety of advantages to automakers and drivers themselves. Let's examine the most important advantages:
1. Weight Reduction
Aluminum weighs about 60% less than steel. This lightening of the vehicle accelerates the vehicle, reduces emissions overall, and saves fuel. Between a 7% improvement in fuel efficiency and a 10% reduction in weight in a vehicle.
2. Improved Fuel Efficiency & Reduced Pollution
Lightweight aluminum components make cars travel further on a single tank of fuel and reduce greenhouse gases. As more and more regulations accumulate globally, aluminum plays an important role in the solution to allow them to do just that.
3. Corrosion Resistance
Aluminum also naturally occurs in the form of a thin outer oxide layer that is extremely corrosion and rust-resistant—a characteristic vital to the car's existence.
4. High Strength-to-Weight Ratio
Aluminum alloys are also produced with higher strength without a weight penalty. This is utilized in structural parts for impact and stress resistance, i.e., crash management systems.
5. Recyclability
Aluminum does not rust and is 100% recyclable. Moreover, roughly 75% of all the aluminum ever made still exists. That minimizes environmental degradation and cost of production by massive proportions.
6. Thermal & Electrical Conductivity
The high heat dissipation property of aluminum has made it the preferred material to be utilized in heat exchangers, motor components, and electric vehicle battery casing. It also keeps temperature-sensitive components at arm's length.
Applications of Aluminum in Motor Vehicles
The application of aluminum in motor vehicles is not limited to one component. It reaches from the powertrain, body, and interior to safety gear to the chassis.
1. Body-in-White (BIW)
It is the mechanical setup of the car. More advanced application of aluminum is being used by manufacturers in:
- Doors
- Hoods
- Fenders
- Roof panels
- Trunk lids
- Aluminum BIW lowers the centre of gravity and optimizes handling.
2. Suspension and Chassis
Parts such as steering knuckles, control arms, subframes, and cross-members capitalize on the strength and weight-reduction advantages of aluminum that minimize ride harshness and deliver better performance.
3. Engine Parts
Aluminum is found in widespread use in:
- Engine blocks
- Cylinder heads
- Oil pans
- Pistons
Its heat conductivity helps in engine heat management, while its light weight reduces the vehicle structure loading.
4. Drivetrain and Transmission
Differential and transmission cases are usually cast in aluminum since they are very intricate in shape and need to be built in a way that they can dissipate the heat.
5. Heat Exchangers
Aluminum is used to its full extent in radiators, intercoolers, and condensers in a bid to make use of its permissible thermal conductivity and corrosion resistance.
6. Wheels
Light weight, better appearance, and better response to braking as a result of saving unsprung weight are offered through the use of aluminum alloy wheels.
7. Crash Management Systems
Front and rear crash boxes, bumper beams, and side-impact bars of extruded aluminum possess crash energy-absorbing characteristics and may provide enhanced occupant protection.
8. Electric Vehicles (EVs)
Aluminum has a very crucial role to play in EVs in:
- Battery enclosures
- Light-weight structures
- Motor mounts Heat sinks
- Lightening EVs renders diversity of batteries a significant marketing benefit.
Challenges and Considerations
There are several benefits of aluminum, but there are certain challenges:
- Cost: Aluminum is comparatively more costly than steel as a raw material as well as a processed material.
- Repair Difficulty: It is usually associated with skilled labour and machinery in replacing or repairing aluminum components.
- Joining Techniques: Welding aluminum is a more complex process involving sophisticated methods like MIG or laser welding compared to steel's spot welding.
- Work Hardening: Aluminum hardens quickly when it is cold-worked and, accordingly, complicates some of the forming operations.
But decades of increasing demand and manufacturing technology advances are worn down.
Conclusion
Aluminum automotive parts are no stranger—They're a motor vehicle technological breakthrough. From fuel efficiency and lightweighting to safety enhancement and assistance toward sustainability, aluminum provides a singular set of advantages. Although there are still some challenges, the advantage in the long run far surpasses the cost.
As production processes improve and recycling lowers the cost of production, the domination of the auto industry by aluminum will be maintained only at an expedited rate. In the lighter, smarter, and greener car world, aluminum is spearheading the revolution—a piece at a time.