Precision in Motion: How Automation Equipment CNC Parts Drive Industrial Innovation
Explore how automation equipment CNC parts drive efficiency and precision in modern manufacturing. Learn about their types, materials, applications, and future trends in smart factories.
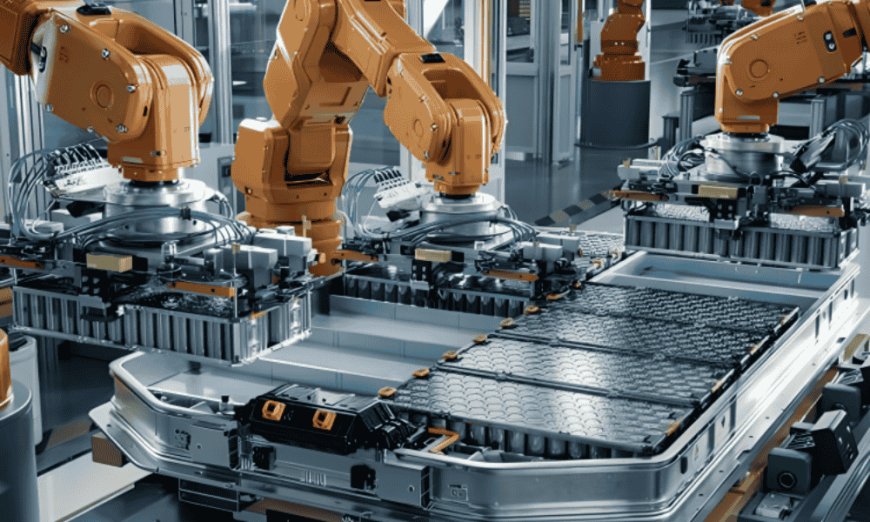
In the modern age of smart manufacturing, precision, reliability, and scalability define success. As industries increasingly automate processes to reduce errors and enhance productivity, the components behind these systems are more critical than ever. Among these, automation equipment cnc parts stand at the forefront—fueling the accuracy and consistency required to power intelligent machines, robotics, and control systems.
This article takes a deep dive into how CNC-machined parts support industrial automation, what types of parts are commonly used, how they’re made, and why they are indispensable in the era of Industry 4.0.
What Are Automation Equipment CNC Parts?
Automation equipment CNC parts are high-precision mechanical components manufactured through computer numerical control (CNC) machining, specifically designed for use in automated systems. These systems may include robotic arms, conveyor systems, industrial packaging lines, pick-and-place machines, and other equipment requiring precise and reliable performance.
Key characteristics of CNC parts for automation include:
-
Tight dimensional tolerances
-
High material durability
-
Compatibility with motion systems
-
Repeatable performance in demanding environments
These components are not off-the-shelf but typically custom-engineered for integration into specialized automated machinery.
CNC Machining Explained
CNC machining is a subtractive manufacturing process in which computer-guided machines remove material from a workpiece to form desired shapes. CAD (Computer-Aided Design) files are used to create CAM (Computer-Aided Manufacturing) toolpaths, guiding tools like lathes, mills, drills, and grinders.
Common Operations Include:
-
CNC Milling: Creates slots, holes, and complex contours
-
CNC Turning: Ideal for cylindrical parts like shafts and bushings
-
Drilling and Tapping: Used for holes, threads, and fastener placement
-
Grinding: Achieves ultra-smooth finishes and tight tolerances
Each operation plays a role in producing precision parts used in industrial automation.
Importance of CNC Parts in Automation Systems
Automated machines are only as good as the components they rely on. CNC-machined parts ensure each subsystem functions with minimal error, reduced maintenance, and optimal energy efficiency.
Key Advantages:
1. Unmatched Precision
Automation requires exact alignment between moving parts. CNC machining delivers tolerances as tight as ±0.001 inches, enabling seamless mechanical coordination.
2. Durability and Reliability
CNC parts are often made from materials that can withstand high loads, heat, and chemical exposure, ensuring long service life in challenging environments.
3. Speed and Scalability
Once programmed, CNC machines can run continuously to produce identical parts at scale, supporting large manufacturing operations without delays.
4. Design Flexibility
From prototyping to full-scale production, CNC machining supports design iterations, rapid changes, and part customization with ease.
Common Automation CNC Parts
Different automation systems require different CNC components. Here are the most common types found in industrial settings:
1. Shafts and Spindles
Used for rotating assemblies and load transmission. Require perfect balance and concentricity.
2. Bearing Housings
Support rotating components and minimize friction. Must fit with micrometer precision.
3. Sensor Brackets
Mount proximity, optical, and feedback sensors to exact positions for proper machine control.
4. End Effectors and Grippers
These robotic elements handle and manipulate objects on the production line. Made from lightweight and durable materials like aluminum or titanium.
5. Custom Fixtures
Used to align, hold, or support components during assembly, welding, or inspection.
Suitable Materials for Automation CNC Parts
The performance of a CNC part largely depends on the material from which it is made. Some of the most commonly used materials include:
-
Aluminum: Lightweight, corrosion-resistant, and cost-effective
-
Stainless Steel: Offers excellent strength, hygiene, and temperature resistance
-
Tool Steel: Ideal for wear-resistant components like dies and punches
-
Plastics (Delrin, Nylon, PEEK): Used where low weight and friction are critical
-
Titanium: High strength-to-weight ratio and corrosion resistance
Material choice depends on application factors such as load, temperature, exposure, and motion frequency.
Industries That Depend on Automation Equipment CNC Parts
1. Automotive
Automated welders, assembly lines, and material handling systems use CNC parts for frames, arms, and sensor mounts.
2. Electronics
High-speed automated pick-and-place systems for PCBs rely on miniaturized, accurate CNC parts to handle delicate components.
3. Aerospace
Automated inspection systems, drilling machines, and robotic arms used in aircraft assembly require high-strength precision components.
4. Medical Devices
Surgical instrument manufacturing and cleanroom assembly use CNC parts made from sterilizable and biocompatible materials.
5. Food and Beverage
Packaging and bottling automation use stainless steel parts to meet hygiene and corrosion resistance standards.
Choosing a Reliable CNC Machining Partner
Not all CNC providers are equal. For automation applications, consider a partner that offers:
-
Advanced Machinery: 5-axis CNC systems for complex geometries
-
Tight Tolerance Expertise: Proven capability in producing parts within microns
-
Material Variety: Support for metals, plastics, and alloys
-
Rapid Turnaround: Capable of meeting urgent production schedules
-
Quality Control Systems: In-house inspection with CMM and surface testing tools
Future Trends in CNC Machining for Automation
1. Integration with IoT
Parts are increasingly being embedded with smart sensors that collect and relay operational data for real-time monitoring.
2. Digital Twin Validation
Before production, digital replicas simulate how CNC parts perform in virtual automation systems, minimizing design errors.
3. Hybrid Manufacturing
Combining CNC machining with 3D printing allows manufacturers to optimize for weight, performance, and cost—especially for complex internal geometries.
4. Sustainable Machining
CNC shops are adopting eco-friendly practices such as dry machining, coolant recycling, and energy-efficient spindle motors.
Conclusion
As manufacturing continues to automate, the demand for reliable, precision-engineered components grows. Automation equipment CNC parts are at the heart of this movement ensuring systems operate smoothly, safely, and without interruption. From aerospace to food processing, these parts enable machinery to perform with confidence and precision.
By working with an experienced CNC machining provider, manufacturers can ensure their automation systems meet today’s challenges and are ready for tomorrow’s innovation. Whether you're scaling up production or optimizing an existing line, investing in quality CNC parts is a step toward operational excellence.