Drilling Disaster Prevention: Avoiding Costly Mistakes in Borehole Machine Selection
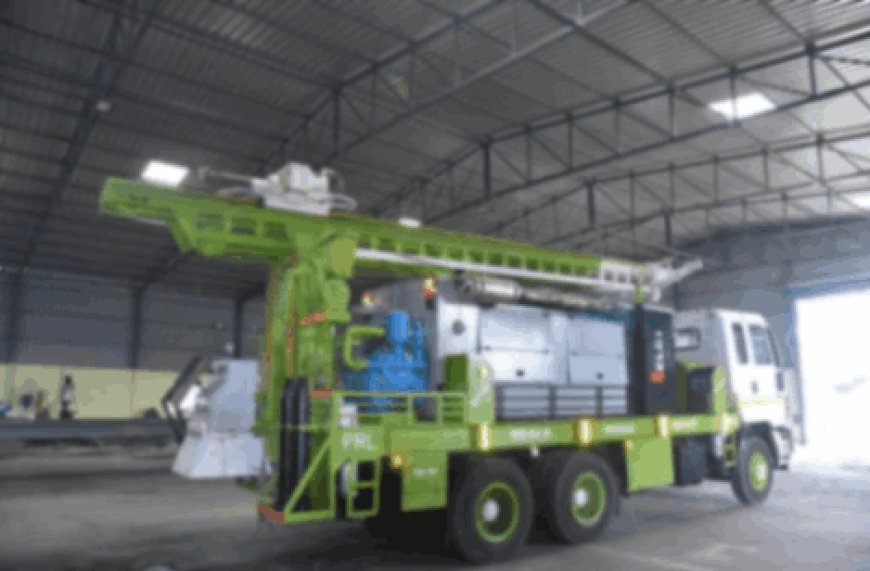
One of the most important choices in mineral exploration, geothermal installations, and water access projects is choosing the appropriate borehole drilling equipment. Unfortunately, many professionals commit mistakes in the candidate selection process, which would otherwise be easy to avoid, yet lead to a significant loss of money, schedule delays and operational inconveniences. These mistakes are common in rash decision-making or unsuccessful research, or in the inaccurate interpretation of project specifications and equipment capabilities. Besides in the early stages of disappointment, poor selection of equipment may cause the production to drop, the burden of maintenance to increase, and even cause the failure of the project. Learning about the common mistakes in selection will make it possible to avoid expensive mistakes that can destroy the projects and damage the professional reputation. In order to choose equipment wisely, one must be aware of potential hazards that might deceive unsuspecting purchasers in addition to knowing what to look for in a borehole drilling machine.
1.Miscalculating Drilling Depth Requirements and Geological Challenges
Underestimating the necessary drilling depth or neglecting to sufficiently evaluate the geological conditions at project locations are two of the most basic mistakes. Instead of taking into account maximum needs or difficult formations that require additional power and capability, many customers choose equipment based on typical drilling depths. Shallow-rated machinery cannot penetrate to a longer depth, leading to poor equipment, holes that were not completed, and degradation of the project. Moreover, the selection of equipment which is not suitable to certain types of rocks, hardness or even groundwaters is a result of disregarded geological surveying or study of the soil composition. Drilling techniques, bit types, and machine capabilities vary depending on the formation. Customers that forego geological evaluation frequently find that the machine they have selected is unable to effectively penetrate anticipated rocks.
2.Overlooking Local Climate Conditions and Environmental Factors
Drilling machine performance is greatly impacted by environmental elements, however many consumers overlook climatic considerations when making selections. The hydraulic systems, engine performance efficiency, and reliability of the machines are influenced by areas of variation in elevation, high temperatures, humidity, dust, etc. Machines designed to work in a temperate climate may not work well in tropical conditions that are high-humidity and seasonally brutal. Conversely, appliances that can operate under a hot environment can not work properly in a cold environment that is at temperatures below freezing point. The machines used that may be standard may lack the sealed parts and certain filtering systems that dust and sand environments in dry areas stretching across vast expanses would require.
3.Inadequate Budget Planning and Hidden Cost Oversights
Another frequent mistake that puts a burden on finances and unfairly restricts equipment possibilities is budget miscalculations. Many purchasers ignore complete ownership costs, such as transportation, installation, training, maintenance, and operating costs, in favor of concentrating just on the purchase price. The true cost of equipment can be greatly raised by unstated expenses such import taxes, permits, import levies, and fees for regulatory compliance. Inadequate funding for maintenance tools, operator training, and spare parts also results in continuous financial strain. Certain buyers underestimate the impacts of depreciation on cash plans, risk coverage requirements, and expenditure on financing. The operational costs of fuel consumption, maintenance schedule and availability of spare parts should be factored in budget estimates. Emergency repair cost and downtime costs may also have a great impact on the economics of the project under conditions it is not properly forecasted.
4.Ignoring Operator Skill Levels and Training Requirements
When drilling equipment are chosen without taking into account the operator's experience or training needs, operational challenges and safety issues frequently result. Advanced features on complex machinery may be beyond the capability of the operator, leading to ineffective operation, equipment damage, or safety problems. On the other hand, excessively basic equipment may result in underutilization of highly qualified personnel, limiting potential production. Machine selection options should be influenced by training needs, prices, and availability, particularly in distant areas with restricted training access. Certain equipment need in-depth training courses or certain certificates, which might not be easily accessible. The availability of training materials, technical documentation quality, and language hurdles all affect the success of operator development.
5.Disregarding Parts Availability and Service Network Coverage
Failure to investigate the availability of spare parts and comfort of service franchises is one of the significant errors that may cause sufficient downtime and overvalued operating costs. In certain machine brands or models, available parts may be limited in remote regions or regions where industrial infrastructure is poorly developed. Timelines and expenses associated with the purchase of parts can be greatly impacted by import limitations, exchange rate volatility, and shipment delays. Some firms lack sufficient local representation in particular areas or have small worldwide distribution networks. Manufacturers and geographical areas differ greatly in terms of service technician availability, response times, and technical proficiency levels. Using approved service locations that are unavailable or inconveniently situated may be required under warranty service requirements.
6.Misjudging Transportation and Site Access Requirements
When choosing a machine, transportation and site access issues are usually disregarded, which results in costly fixes or operating restrictions. Large machines may need specific permissions, route design, and transportation equipment, all of which raise project costs considerably. Narrow roads, weight constraints, overhead clearances, or difficult terrain can all make it difficult for some machinery to reach work areas at drilling sites. Transportation-related disassembly and reassembly needs may lengthen setup times and complicate tasks. Additionally, the needs for site preparation change greatly depending on the size and design of the equipment. Environmental impact assessments or specific permits may be needed in some places for the operation or shipment of equipment. Decisions on which machines to use can be influenced by the needs for fuel storage and transportation in remote areas.
7.Failing to Verify Manufacturer Credibility and Support Quality
Long-term equipment satisfaction is greatly impacted by manufacturer reputation and support quality, however many consumers base their decisions largely on pricing and specs without thoroughly evaluating suppliers. The applicability of their products and the quality of their service may be impacted by certain manufacturers' lack of familiarity with particular applications or geographical areas. Manufacturers' capacity to maintain parts manufacturing, fulfill warranties, and offer continuing assistance is influenced by their financial stability. References from customers, the standing of the industry, and performance history in related applications offer important information about the dependability of manufacturers. Technical support, training courses, high-quality documentation, and attentiveness to client needs are all examples of support quality. Despite their superior equipment design, some manufacturers offer subpar after-sales service, which makes operations difficult.
Conclusion
In order to prevent these common errors, discipline, endurance, and careful assessment process accounting of all the relevant variables that affect the choice of drilling rig machine is required. To effectively make informed decisions that facilitate successful completion of a project long term, prudent customers invest their time in carrying out research, physical tours, and analysis of the suppliers. Identification of potential risks and implementation of proper strategies to protect the investments protects the investments and ensures that the equipment to be used meets the needs of the project requirements and provides a reliable market service.